Case Study: How Preventive Maintenance Saved a Denver Business Thousands
Introduction to Preventive Maintenance
In today's competitive business environment, maintaining operational efficiency is crucial. Many businesses are turning to preventive maintenance as a strategic approach to minimize downtime and control costs. This method involves regular and systematic inspections, detection, and correction of incipient failures before they occur or develop into major defects.
In Denver, one local business has reaped significant benefits from implementing a preventive maintenance strategy. This case study explores how this approach not only saved the company thousands of dollars but also enhanced its overall operational efficiency.
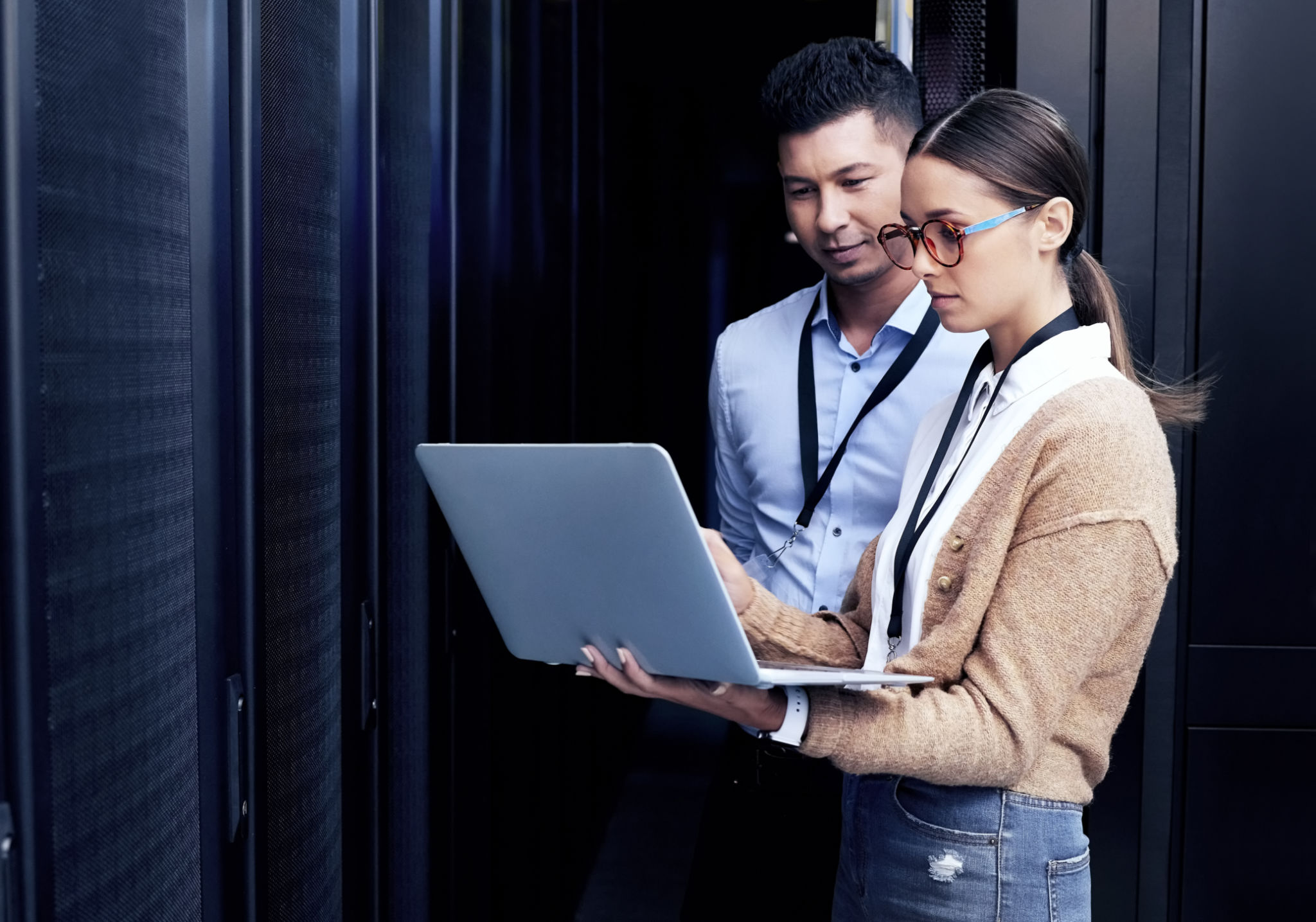
The Challenge: Frequent Equipment Breakdowns
The Denver-based business, operating in the manufacturing sector, faced frequent equipment breakdowns, leading to unexpected downtimes and costly repairs. These disruptions not only affected their production schedule but also strained their relationship with clients due to delayed deliveries.
Regular reactive maintenance was proving inadequate to handle the issues, prompting the management to explore more proactive solutions. They needed a strategy that would not only mitigate these disruptions but also optimize their maintenance processes.
Implementing a Preventive Maintenance Plan
The company decided to implement a comprehensive preventive maintenance plan. This involved scheduling regular maintenance checks and servicing for all critical machinery and equipment. The plan included:
- Routine inspections and cleaning
- Timely replacement of worn-out parts
- Systematic lubrication of machinery components
- Regular calibration of equipment
By addressing potential issues before they escalated, the company aimed to enhance the reliability and longevity of their machinery.

The Immediate Benefits
After just a few months of implementing the preventive maintenance plan, the company observed significant improvements. The frequency of equipment breakdowns reduced dramatically, which in turn minimized downtime. The staff could focus more on production rather than troubleshooting unexpected issues.
Moreover, the company noticed a decrease in repair costs. By replacing parts before they failed completely, they avoided more extensive damage and costly emergency repairs.
Long-Term Impact on Business Operations
In the long term, the preventive maintenance approach led to substantial financial savings. The cumulative savings from reduced downtime and repair costs amounted to several thousand dollars annually. Furthermore, improved equipment reliability enhanced their production capacity, enabling them to meet client demands more efficiently.
The company also reported improved employee morale as staff felt less stressed about unexpected breakdowns and could work in a more stable environment.
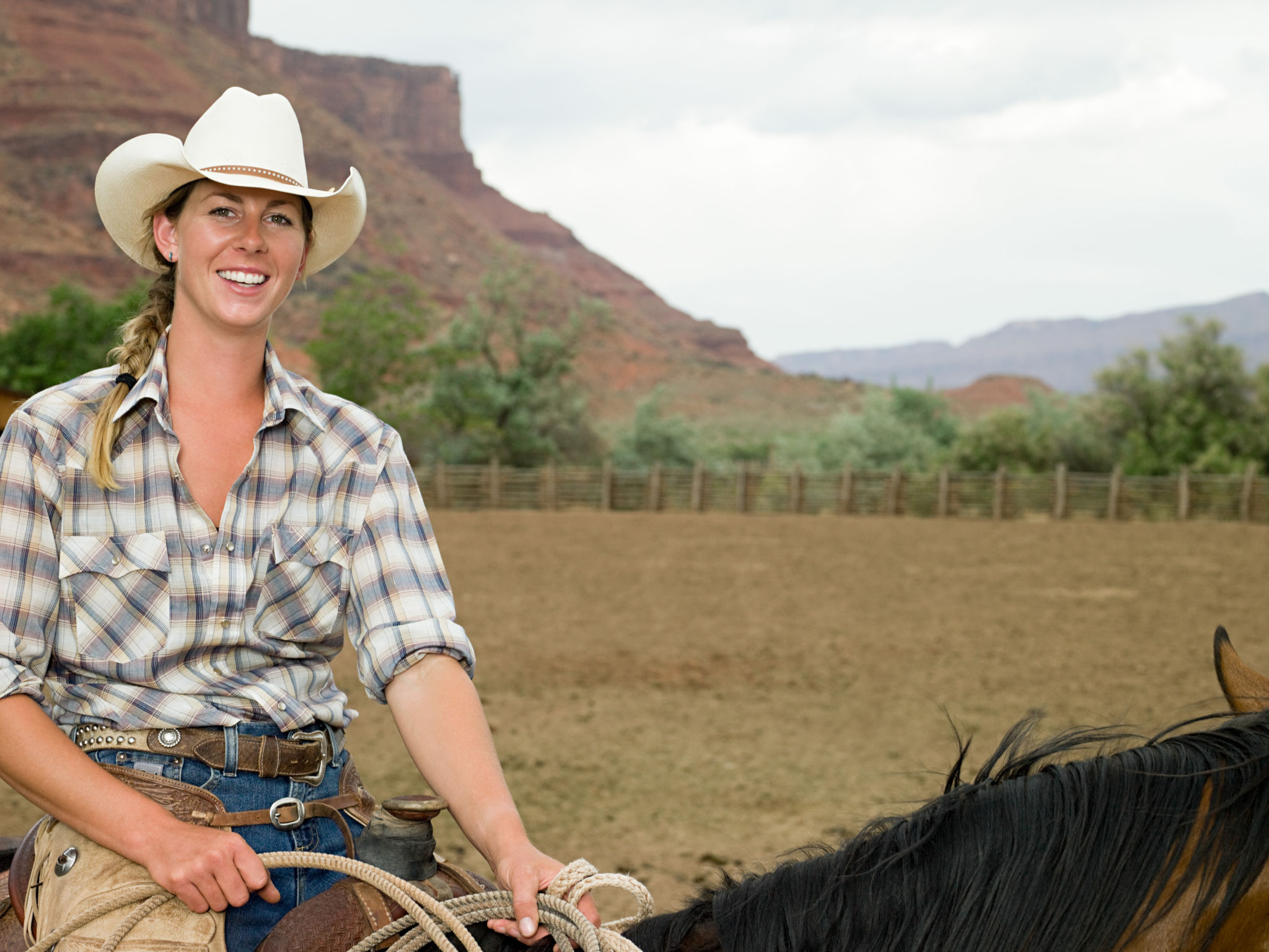
Conclusion: A Proactive Approach Pays Off
This case study highlights the importance of adopting a preventive maintenance strategy for businesses reliant on machinery and equipment. By investing in regular maintenance checks and addressing potential issues proactively, companies can save significant amounts in repair costs and operational downtimes.
For businesses in Denver and beyond, preventive maintenance is not just a cost-saving measure but a strategic investment in long-term operational success. By ensuring equipment reliability, companies can improve productivity, maintain customer satisfaction, and ultimately stay ahead in the competitive market landscape.